Uncategorized
All about Types of material for Wall Construction- Masonry Block
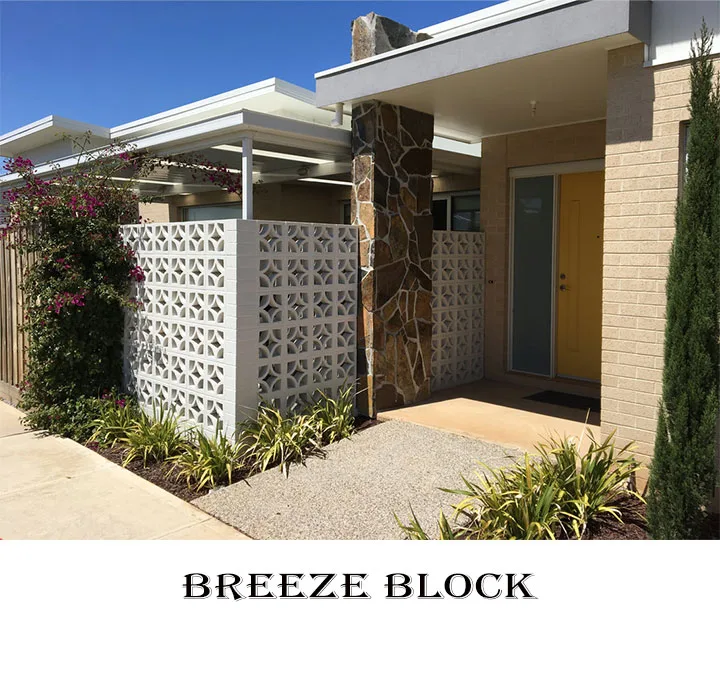
Masonry blocks are the main component of the wall. In 21 century, construction materials are changed instead of traditional materials. Here we will discuss all wall material mainly brick or block, which is the main component of a wall.
Many kinds of walls for a building are the Main wall, partition wall, retaining wall, boundary wall, parapet wall, etc.
Size, Shape, and strength vary for different types of walls. For the Partition wall, a minimum strength block is required which is safe for bearing self-load and the retaining wall block will be good under vertical and horizontal pressure strong.
Table of Contents
Further, we discuss the type of block used for different purposes available in the market.
Type of masonry block
- Based on the material of the block
- Based on shape of block
- Based on Manufacturing Type of block
Type of Masonry Block Based on Material of Block:
- Concrete block
- Fly Ash block
- AAC block
- Cinder block
1. Concrete Block
Masonry blocks made with concrete mortar only are concrete blocks. Concrete mortar consists of cement, sand, and aggregate. Concrete blocks are available in different sizes in the market. The strength of mortar decides block strength.
Read Also: Concrete blocks: Types, Tests Pros & manufacturing process
2. Fly Ash Block
Masonry blocks are made with concrete mortar which includes fly ash called fly ash Block. Fly ash is a waste product of coal thermal power plants. The use of fly ash in blocks makes an environment-friendly product and reduces the weight of the block.
3. AAC block
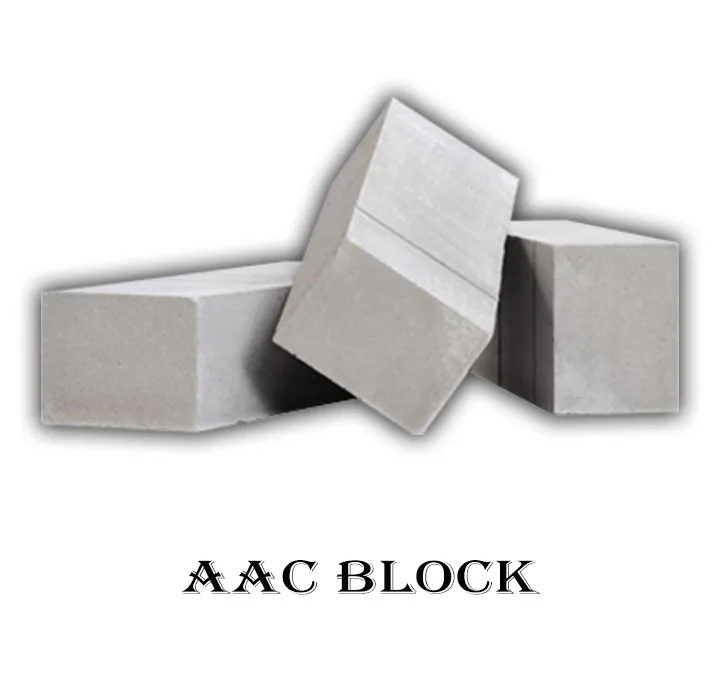
AAC (Autoclave aerated concrete) Block is a new kind of lightweight block used in multistory buildings. AAC blocks are not strong enough like clay bricks or concrete blocks, so used only in buildings where columns and beams are provided for load transfer, and blocks are used for partition walls only.
4. cinder block
Cinder blocks are similar to concrete blocks but are made from industrial waste materials such as coal cinders.
Type of Masonry Block Based on Shape of Block:
- Solid Block
- Hollow block
- Key/ interlock Block
- Beltis block
- Breeze block
1. Solid Block
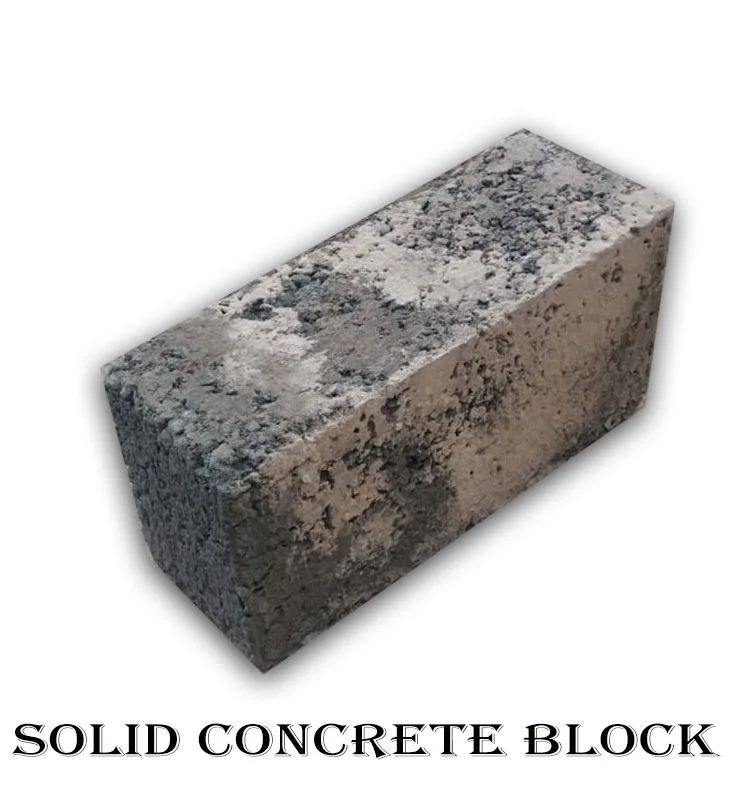
A solid block is completely dense and has no open spaces inside it. Solid blocks are typically used in load-bearing walls or other structural applications where strength and durability are essential.
Solid blocks are available in a variety of sizes and shapes, including standard rectangular blocks, and corner blocks. Used in the construction of foundations, retaining walls, and structural walls.
2. Hollow Block
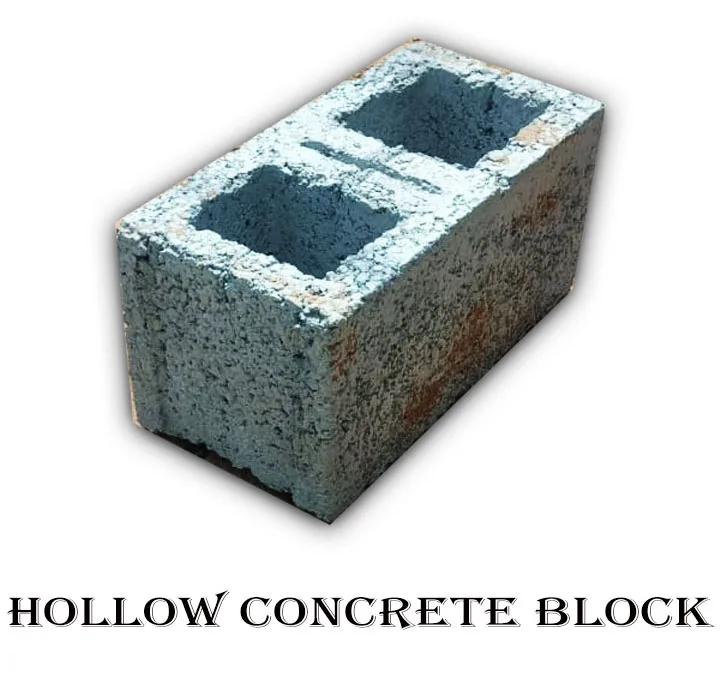
Hollow blocks are a type of masonry block that have one or more hollow cores or voids running through the middle. These voids can be either circular or rectangular in shape and are usually filled with a material such as concrete or insulation to improve the block’s strength and insulation properties.
Hollow blocks are commonly used in construction for non-load-bearing walls and partitions, as well as for decorative purposes.
3. Key/ interlock Block

Interlocking masonry blocks are a type of building block that is designed to fit together like puzzle pieces, without the need for mortar or other adhesives. These blocks have unique shapes that interlock with one another, creating a strong, stable, and secure connection. Interlocking masonry blocks are often used in construction for retaining walls, garden walls, and other landscaping projects, as well as for residential and commercial buildings.
One of the main advantages of using interlocking masonry blocks is their ease of installation. Because they do not require mortar, they can be quickly and easily installed by a trained professional or even a DIY enthusiast. This can save time and money during the construction process.
5. Breeze Block
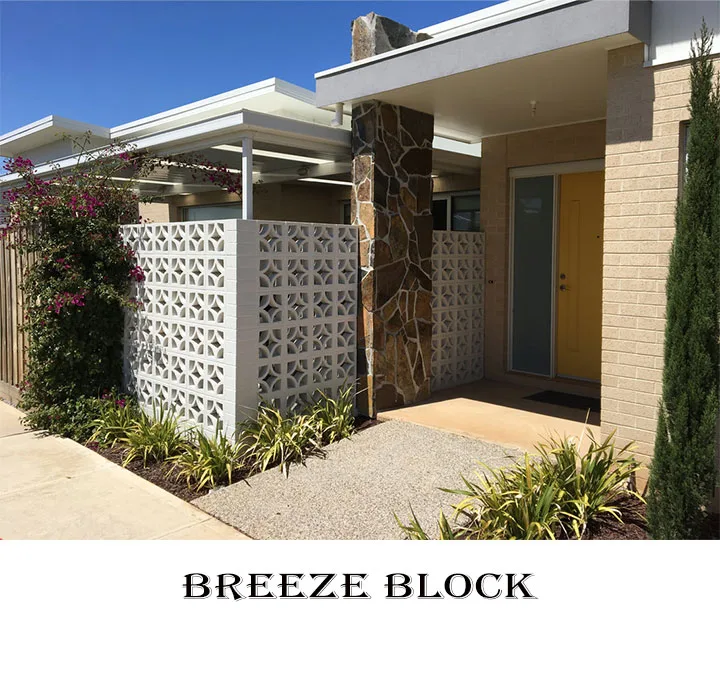
Breeze blocks, also known as decorative blocks, have decorative patterns and are commonly used in architectural projects.
Read also: Needs of Many New City: Urban Development in India
Type of Masonry Block Based on Manufacturing of Block:
- Hydraulic pressed block
- Vibrated block
- Autoclave heated block
1. Hydraulic-pressed block
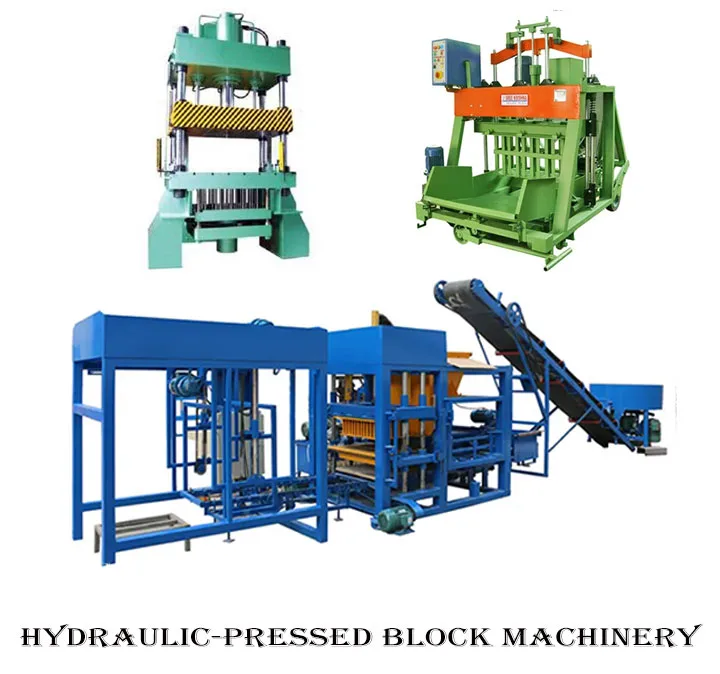
A type of masonry block that is manufactured using hydraulic pressure to compress and shape the block. These blocks are typically made from a mix of cement, sand, and other aggregates, which are mixed with water and then placed into a mold. The mold is then subjected to hydraulic pressure, which compacts the mixture and creates a dense, uniform block.
Advantages of using hydraulic pressed blocks
- Resistance to moisture and weathering.
- Uniform size and shape
- The dense, tightly compacted nature of these blocks makes them less susceptible to moisture intrusion and damage from freeze-thaw cycles.
- Fire-resistant, making them a good choice for construction projects where fire safety is a concern.
Disadvantages of using hydraulic pressed blocks
- Low insulation property
- Expensive due to the heavy machinery for manufacturing.
2. Vibrated block
During the manufacturing process, the concrete mixture is poured into a mold and then subjected to high-frequency vibration, which compacts the mixture and removes any air pockets. This creates a dense, uniform block that is stronger and more durable than other types of masonry blocks.
Advantages of using vibrated masonry blocks
- Good strength and durable
- Dense, well compacted
- less prone to cracking, chipping, or other forms of damage
- good insulation properties.
How to calculate the number of blocks?
The number of blocks depends on mainly two factors:
- Size of plot
- Size of the blocks
Assume A wall 8″ thick, 10′ long, and 9 feet high have to be constructed. And the size of block is 16″ X 8″ X 6″
- Leave the width of the block and thickness of the wall which is the same 8″.
- Area of wall = 10’*9′ = 90 square feet.
- Area of block = 16″*6″ = 96 square inch = 0.667 square feet.
- Number of blocks = area of wall/area of the block
- Number of blocks = 90/0.667 = 134.93
- Approx 135 blocks(16″x8″x6″) for 90 square feet of work required.
Uncategorized
11 – Aggregate Test -All Type & Importance
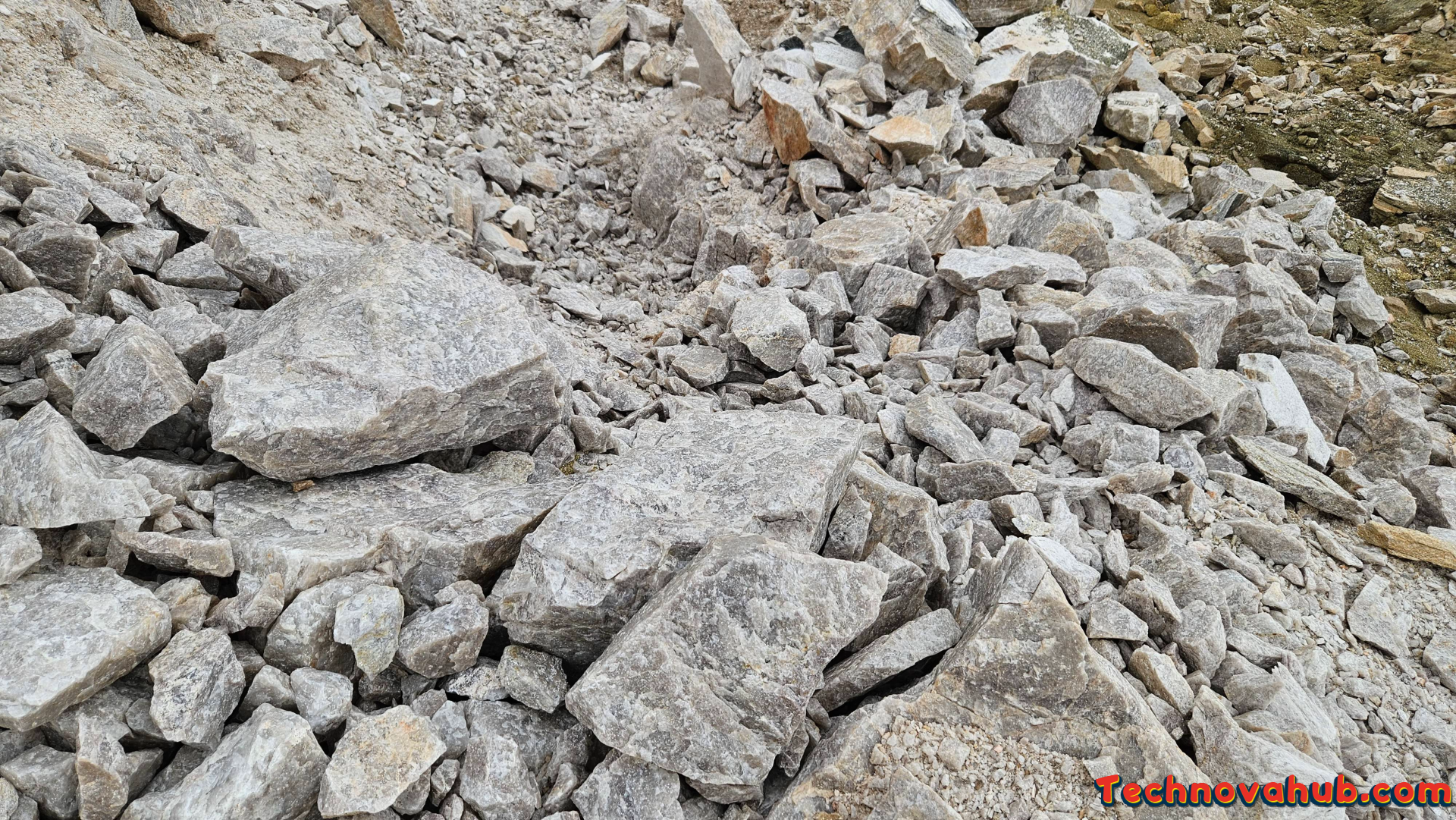
Aggregate test is the most important substance in the construction industry. The strength of the structure after joint strength depends on the strength of the aggregate.
Aggregate indeed plays a crucial role in the construction industry, particularly in the production of concrete. Concrete is a fundamental building material used in various construction projects, and its strength and durability are significantly influenced by the quality of its components, including aggregate.
Required characteristics of aggregate
The study of aggregate can improve the strength of construction as well as money. Here are some key points about the importance of aggregate test in construction:
- Strength and Durability: Aggregates are the primary component in concrete, constituting about 60-75% of the total volume. The properties of the aggregate, such as its strength and durability, directly impact the overall strength and durability of the concrete structure.
- Load-Bearing Capacity: Aggregates provide the bulk and rigidity to concrete, contributing to its load-bearing capacity. The arrangement of aggregates in the mix affects the compressive strength of concrete, which is crucial for supporting structural loads.
- Economy: Properly graded and high-quality aggregates can enhance the workability of concrete mixtures, allowing for more economical use of cement. This is important as cement is typically a more expensive component of concrete. A well-designed mix with the right proportion of aggregate can optimize the use of cement without compromising strength.
- Volume Stability: The expansion and contraction of concrete due to temperature changes and moisture variations can be influenced by the type and quality of aggregate used. Aggregates that are resistant to changes in volume help ensure the long-term stability of the concrete structure.
- Bonding with Cement Paste: The interface between the aggregate particles and the cement paste (the glue that holds concrete together) is critical. Proper bonding is necessary to achieve the desired strength and durability. The surface characteristics of the aggregate can impact this bonding.
- Shape and Size: The shape and size of aggregate particles also play a role. Well-graded aggregates with a variety of sizes can result in a denser and more workable mix. The shape of the particles can affect the surface area and, consequently, the amount of cement paste needed for adequate bonding.
Above all parameters are used to identify aggregate before use on-site in construction.
Type of Aggregate test :
- Particle Size Distribution (Gradation Test):
- Purpose: Determines the distribution of particle sizes within an aggregate sample.
- Method: Sieves of different sizes are used to separate and measure the particles.
- Shape and Texture Tests:
- Flakiness and Elongation Index Test:
- Purpose: Assesses the shape characteristics of aggregate particles.
- Method: Measures the ratio of the elongated or flaky particles to the total mass.
- Angularity Number Test:
- Purpose: Quantifies the angularity of aggregate particles.
- Method: Involves measuring the volume of voids between angular particles.
- Flakiness and Elongation Index Test:
- Specific Gravity and Absorption Test:
- Purpose: Determines the specific gravity and water absorption of the aggregate.
- Method: Involves measuring the weight of the aggregate in air and in water to calculate specific gravity and absorption.
- Bulk Density and Voids Test:
- Purpose: Measures the density and void content of aggregate.
- Method: Involves determining the bulk density and calculating the percentage of voids in the aggregate.
- Soundness Test:
- Purpose: Evaluates the resistance of aggregate to disintegration due to weathering.
- Method: Aggregates are subjected to cycles of wetting and drying in a sodium sulfate or magnesium sulfate solution.
- Los Angeles Abrasion Test:
- Purpose: Measures the resistance of agSogregate to abrasion and impact.
- Method: Aggregates are placed in a drum and rotated, causing abrasion and impact on the particles.
- Crushing Value Test:
- Purpose: Determines the aggregate’s resistance to crushing under a gradually applied compressive load.
- Method: Aggregates are subjected to a specified load and the percentage fines generated is measured.
- Impact Value Test:
- Purpose: Measures the aggregate’s resistance to sudden impact.
- Method: Aggregates are subjected to a standard impact test using a testing machine.
- Moisture Content Test:
- Purpose: Determines the moisture content of aggregates.
- Method: Involves weighing the aggregate before and after drying to calculate the moisture content.
- Alkali Aggregate Reactivity Tests:
- Alkali-Silica Reactivity (ASR) Test: Evaluates the potential of aggregates to react with alkalis in concrete.
- Alkali-Carbonate Reactivity (ACR) Test: Assesses the potential reactivity of carbonate aggregates.
- Organic Impurities Test:
- Purpose: Identifies the presence of organic materials in the aggregate.
- Method: Aggregates are immersed in a solution, and any color change is observed.
IS Code for Aggregate are shown as:
IS CODE | AGGREGATE TEST |
IS 2386 – 8 | Methods of Test for Aggregates for Concrete – Petrographic Examination |
IS 2386-7 | Methods of Test for Aggregates for Concrete, Part VII: Alkali Aggregate Reactivity |
IS 2386-6 | Methods of test for aggregates for concrete: Measuring mortar making properties of fine aggregates |
IS 2386-5 | Methods of test for aggregates for concrete: Soundness |
IS 2386-4 | Methods of test for aggregates for concrete: Mechanical Properties |
IS 2386-3 | Methods of test for aggregates for concrete: Sp. Gravity, Density, Voids, Bulk Density & Water absorption |
IS 2386-2 | Methods of test for aggregates for concrete: |
IS 2386-1 | Methods of test for aggregates for concrete: Particle Size & Shape |
Read Also : Concrete blocks: Types, Tests Pros & manufacturing process
Read also : Most Recommended Is Codes For Aggregates In Construction
Uncategorized
Concrete mixer machine: Guide to Efficient Mixing Equipment
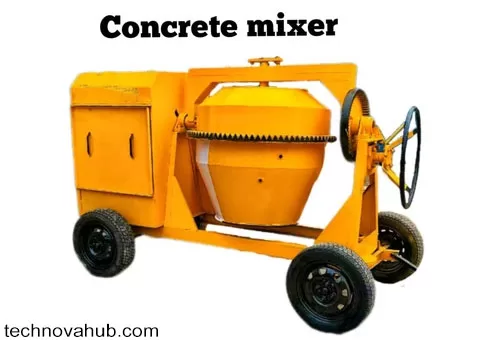
A concrete mixer machine, also known as a cement mixer, is a device used to combine cement, water, and aggregates (e.g., sand, gravel, or crushed stone) to form concrete. This mixing process ensures that the concrete’s components are evenly distributed and results in a homogenous mixture that is suitable for construction purposes.
Table of Contents
Concrete mixers machine come in various sizes and types, but the most common ones are:
Types of Concrete Mixture Machine
1. Drum Mixer:
This is the most common type of concrete mixer machine, where the ingredients are mixed by tumbling them inside a revolving drum. The drum can be tilted to discharge the concrete. Drum mixers can be further classified as:
- Tilting Drum Mixers: The drum can be tilted to pour the concrete.
- Non-Tilting Drum Mixers: The drum is fixed, and the concrete is discharged by opening a chute at the bottom.
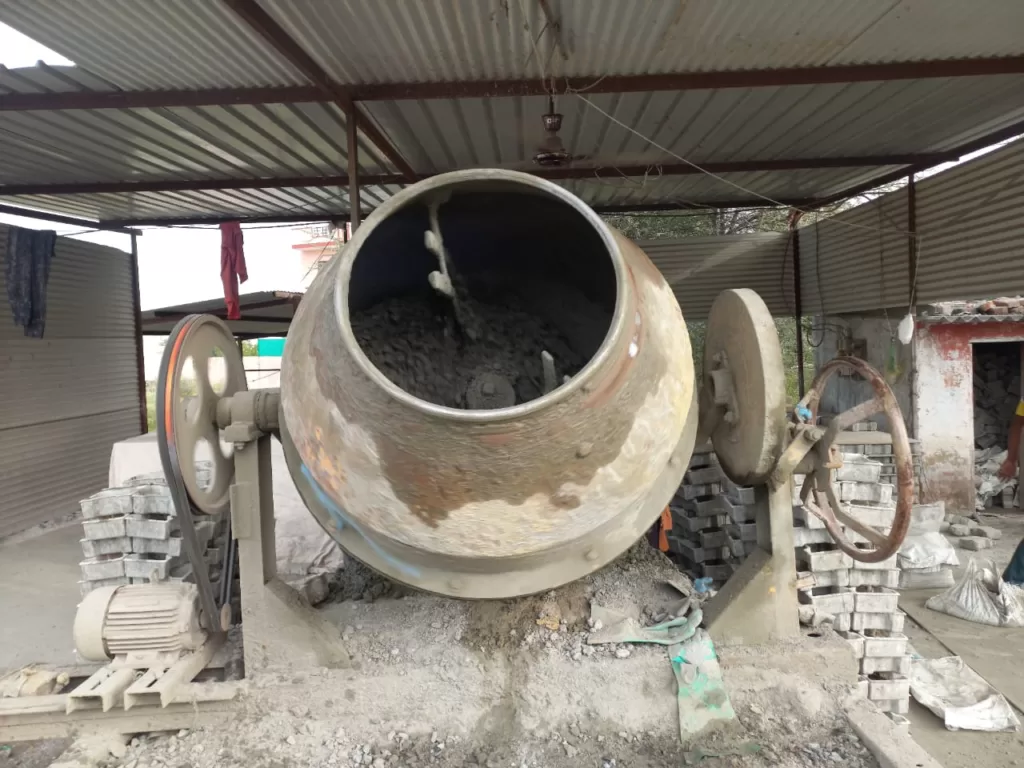
2. Pan Mixer
This type of mixer has a stationary mixing pan and blades that rotate around a vertical axis. The ingredients are mixed as the blades move through the material.

3. Twin Shaft Mixer
This type of mixer has two horizontal shafts with paddles that counter-rotate, ensuring thorough mixing of the materials.
4. Vertical Axis Mixer
In this mixer, the shaft is vertical, and the mixing action is similar to a pan mixer but on a larger scale.
Concrete mixer machines are widely used in various construction projects, including buildings, roads, bridges, and other structures. They are available in different capacities, ranging from small portable mixers suitable for DIY projects to large stationary mixers used in commercial construction.
When operating a concrete mixer machine, it’s essential to follow safety guidelines, wear appropriate protective gear, and ensure that the machine is used and maintained correctly to prevent accidents and ensure optimal performance. Additionally, different types of mixers and concrete formulations may be suitable for specific construction applications, so it’s essential to choose the right equipment and mix design for the project at hand.
Read Also: Best Cement for Paver Block Manufacturing
Reference : Concrete mixer
HOW TO CHOOSE THE RIGHT CONCRETE MIXER machine?
1. Size
Power supply
Durability
portability
Which Concrete Mixture Machine is used Most commonly?
Mostly Drum Mixture machine is used. It is used due to its ease to handle for loading cement, sand, and aggregate as well as unloading concrete. Tilting Drum Mixers are used commonly at small scales. No chute opening is available for unloading, so no cement slurry waste and homogeneous concrete mixture occurs.
What size is to be considered while purchasing a new concrete mixture machine?
When loading and unloading of concrete and material are done by labor manually then choose a capacity of 1.5 bag cement concrete mixture.
What is the price of the RCC Concrete mixer machine?
The concrete Mixture machine costs 50,000 rupees to 2,50,000 rupees. It depends on type of mixture and size of the mixture.
Motor-operated Tilting Drum Mixers costs around 75,000 rupees.
Disclaimer
Please note that the information on technovahub.com is designed to provide general information on the topics presented. The information provided should not be used as a substitute for professional services.
Uncategorized
Optimizing Ventilation and Air Circulation in Architectural Building Design: Enhancing Indoor Comfort and Health
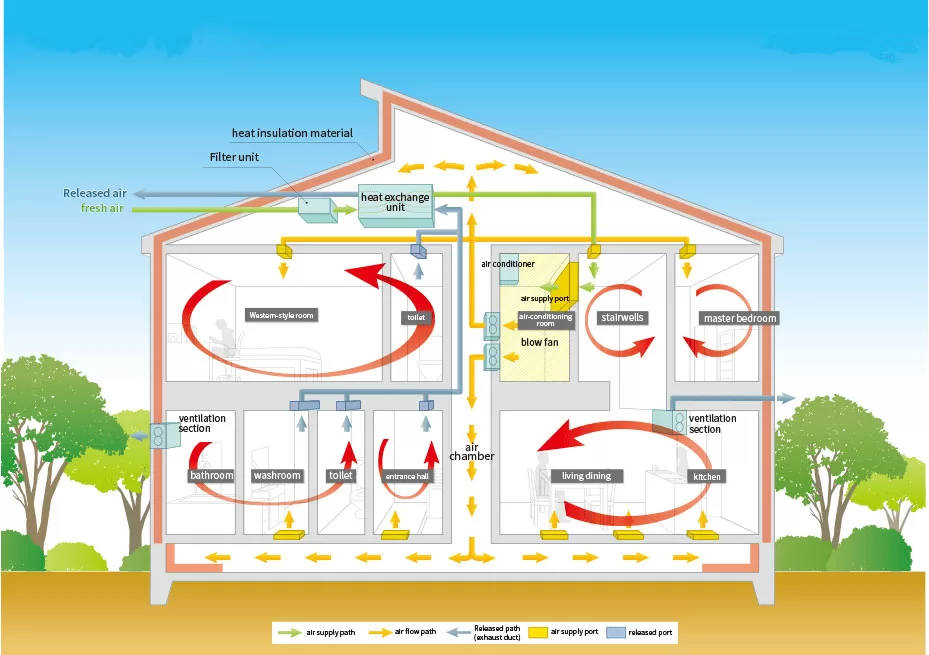
Creating a comfortable and healthy indoor environment is a key consideration in architectural building design. Ventilation and air circulation play a vital role in achieving this goal. In this blog post, we will explore the importance of ventilation and air circulation, discuss key strategies for optimizing these factors, and highlight their impact on indoor comfort and occupant health.
Table of Contents
Importance of Ventilation and Air Circulation
A. Definition and Purpose:
Ventilation refers to the process of exchanging air within a space to maintain indoor air quality and regulate temperature and humidity levels. It involves the intentional movement of air into and out of a building, ensuring a constant supply of fresh air while removing stale air, pollutants, and odors. Air circulation, on the other hand, pertains to the movement of air within a space, promoting even distribution and mixing.
The primary purpose of ventilation and air circulation in architectural building design is to create a healthy and comfortable indoor environment for occupants. By supplying fresh air and effectively circulating it, these factors play a crucial role in maintaining optimal indoor air quality, regulating temperature and humidity, removing contaminants, and preventing the buildup of stagnant air.
B. Benefits of Adequate Ventilation:
Adequate ventilation offers numerous benefits, both for the occupants and the building itself. Some key benefits include:
- Improved Indoor Air Quality (IAQ): Proper ventilation helps remove pollutants, such as volatile organic compounds (VOCs), allergens, and odors, from the indoor environment. This promotes healthier indoor air, reduces the risk of respiratory issues, and enhances overall occupant well-being.
- Enhanced Comfort: Ventilation helps control temperature and humidity levels, preventing the accumulation of heat, moisture, and stuffiness. It ensures a more comfortable living or working environment, reducing the likelihood of discomfort, fatigue, and productivity loss.
- Moisture Control and Mold Prevention: Effective ventilation helps manage moisture levels, particularly in areas prone to high humidity, such as bathrooms and kitchens. By expelling excess moisture, it minimizes the risk of mold growth, which can lead to respiratory problems and structural damage.
- Odor Removal: Proper air exchange through ventilation helps eliminate unpleasant odors caused by cooking, cleaning agents, or other sources. This creates a fresh and inviting indoor atmosphere.
- Combustion Product Removal: Ventilation is crucial for spaces where combustion-based appliances are used, such as kitchens with gas stoves or rooms with fireplaces. It ensures the removal of harmful combustion byproducts, such as carbon monoxide, reducing the risk of health hazards.
C. Role of Air Circulation in Enhancing Indoor Comfort
Air circulation complements ventilation by promoting the even distribution of fresh air throughout a space. It plays a significant role in enhancing indoor comfort in several ways:
- Temperature Regulation: Proper air circulation helps distribute cooled or heated air evenly, reducing temperature variations and creating a more consistent and comfortable environment.
- Reduced Stagnation: Air circulation prevents stagnant air pockets, which can lead to uneven temperatures, poor air quality, and a sense of discomfort. It promotes a fresh and lively atmosphere by constantly moving and refreshing the air.
- Draft Prevention: While adequate air circulation is essential, it should be balanced to avoid uncomfortable drafts. Proper design and placement of air outlets and diffusers can ensure effective circulation without causing direct drafts on occupants.
- Evaporation and Cooling: Air circulation can enhance the effectiveness of natural or mechanical cooling systems by promoting evaporation, aiding in thermal comfort during warmer months.
By understanding the importance of ventilation and air circulation, architects and building designers can incorporate effective strategies to ensure a healthier, more comfortable, and pleasant indoor environment for occupants. These considerations are essential for creating spaces that support well-being, productivity, and overall quality of life.
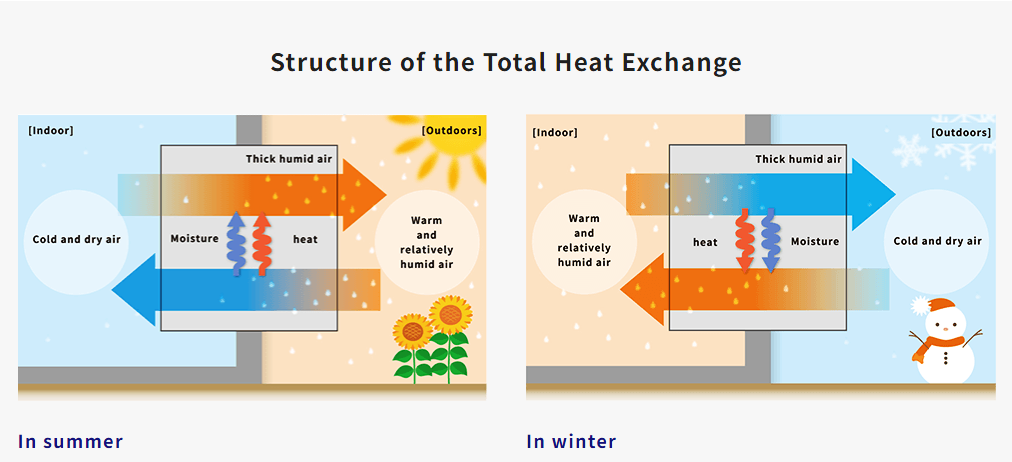
II. Designing Effective Ventilation Systems
A. HVAC Systems Overview
Heating, Ventilation, and Air Conditioning (HVAC) systems are integral to designing effective ventilation systems in buildings. HVAC systems control temperature, humidity, and air quality to create a comfortable and healthy indoor environment. Understanding the components and principles of HVAC systems is crucial in designing an efficient ventilation system.
B. Sizing and Selection of Air Handling Units
Air handling units (AHUs) are central components of HVAC systems responsible for conditioning and distributing air throughout the building. Proper sizing and selection of AHUs are essential to ensure sufficient airflow and ventilation. Factors to consider include the building’s size, occupancy, ventilation requirements, and energy efficiency goals.
C. Ductwork Layout and Distribution
Ductwork plays a critical role in delivering conditioned air to different areas of the building. The layout and design of ductwork should facilitate efficient air distribution and minimize pressure losses. Proper sizing, routing, and insulation of ducts are vital to maintain desired airflow rates and prevent heat gain or loss.
D. Importance of Outdoor Air Intake and Exhaust Systems
Outdoor air intake and exhaust systems are vital components of ventilation systems. Outdoor air intake brings fresh air into the building, while exhaust systems remove stale air and pollutants. The design of these systems should consider factors such as outdoor air quality, pollutant sources, and local regulations to ensure a sufficient supply of fresh air and the effective removal of indoor contaminants.
E. Integration of Ventilation with Heating and Cooling Systems
Integrating ventilation with heating and cooling systems optimizes energy efficiency and comfort. HVAC systems can incorporate various strategies to integrate ventilation, such as:
- Demand-Controlled Ventilation (DCV): DCV adjusts ventilation rates based on occupancy levels, improving energy efficiency by delivering fresh air only when needed.
- Heat Recovery Ventilation (HRV) and Energy Recovery Ventilation (ERV): HRV and ERV systems recover heat or coolness from exhaust air and transfer it to incoming fresh air, reducing energy demand while maintaining ventilation effectiveness.
- Zoning and Variable Air Volume (VAV): Zoning allows for customized ventilation and temperature control in different areas, while VAV systems adjust airflow rates based on specific needs, optimizing comfort and energy efficiency.
Integration of ventilation with heating and cooling systems requires careful coordination and control strategies to ensure effective and balanced air distribution, thermal comfort, and energy conservation.
By paying attention to HVAC system selection, proper sizing of air handling units, well-designed ductwork, outdoor air intake and exhaust systems, and integration with heating and cooling systems, architects can design effective ventilation systems that provide optimal indoor air quality, thermal comfort, and energy efficiency in buildings. These considerations are vital in creating healthy, comfortable, and sustainable indoor environments for occupants.
III. Ensuring Indoor Air Quality (IAQ)
A. Importance of IAQ in Building Design
Indoor Air Quality (IAQ) is a critical factor in building design as it directly impacts occupant health, comfort, and productivity. Poor IAQ can lead to respiratory issues, allergies, fatigue, and decreased cognitive function. Designing ventilation systems that prioritize IAQ helps create a healthy and comfortable indoor environment.
B. Sources of Indoor Air Pollutants
Indoor air pollutants can originate from both internal and external sources. Common sources include:
- Building materials and furnishings: Volatile organic compounds (VOCs) released from paints, carpets, furniture, and adhesives.
- Combustion processes: Gas stoves, fireplaces, and tobacco smoke release pollutants like carbon monoxide and particulate matter.
- Cleaning products and pesticides: Harsh cleaning agents and pesticides can emit harmful chemicals.
- Biological contaminants: Mold, pollen, dust mites, and pet dander contribute to poor IAQ.
- Outdoor pollutants: Pollution from nearby industries, vehicle exhaust, and allergens can infiltrate indoor spaces.
C. Ventilation Rates and IAQ Standards
Ventilation rates play a crucial role in maintaining good IAQ by diluting and removing indoor air pollutants. Adequate ventilation rates depend on factors such as occupancy, pollutant sources, and building type. IAQ standards, such as those set by ASHRAE (American Society of Heating, Refrigerating, and Air-Conditioning Engineers), provide guidelines for ventilation rates to achieve acceptable IAQ levels in various spaces.
D. Filtration Systems and Air Purification Technologies
To enhance IAQ, filtration systems and air purification technologies can be employed:
- Air filters: High-efficiency air filters trap and remove particulate matter, dust, and allergens from the air as it passes through the ventilation system.
- Electrostatic precipitators: These devices use electrostatic charges to capture and remove airborne particles.
- UV germicidal irradiation: Ultraviolet (UV) light can neutralize microorganisms, such as bacteria and viruses, within the ventilation system.
- Ionization systems: Ionizers release ions that attach to and remove airborne pollutants, improving IAQ.
- Activated carbon filters: These filters adsorb gases, odors, and VOCs, improving IAQ by removing chemical contaminants.
The selection and implementation of filtration systems and air purification technologies should be based on the specific IAQ requirements of the building and the types of pollutants present.
By addressing sources of indoor air pollutants, ensuring appropriate ventilation rates according to IAQ standards, and incorporating effective filtration systems and air purification technologies, architects can significantly improve IAQ in buildings. This promotes occupant health, productivity, and overall well-being.
IV. Harnessing Natural Ventilation Strategies
A. Benefits and Principles of Natural Ventilation
Natural ventilation is the process of using natural forces, such as wind and temperature differences, to supply fresh air and remove stale air from a building. It offers several benefits, including:
- Improved IAQ: Natural ventilation brings in fresh outdoor air, reducing the concentration of indoor air pollutants.
- Energy Efficiency: By relying on natural airflow instead of mechanical systems, natural ventilation can reduce energy consumption and associated costs.
- Thermal Comfort: Properly designed natural ventilation can help regulate indoor temperatures and create a comfortable environment for occupants.
- Connection with Nature: Natural ventilation allows occupants to experience the natural elements, fostering a sense of connection with the outdoors.
The principles of natural ventilation involve understanding air movement, pressure differentials, and the design of openings to facilitate the flow of air.
B. Building Orientation and Window Placement Considerations
Building orientation and window placement play a significant role in harnessing natural ventilation. Considerations include:
- Wind Direction: Orienting the building to capture prevailing winds helps facilitate the inflow of fresh air.
- Window Size and Placement: Placing windows strategically to allow for cross-ventilation and capturing prevailing breezes optimizes the effectiveness of natural ventilation.
C. Cross-Ventilation and Stack Effect Utilization
Cross-ventilation is a natural ventilation strategy that involves creating openings on opposite sides of a space to allow air to enter and exit, facilitating air movement. The stack effect takes advantage of the buoyancy of warm air, where warm air rises and escapes through higher openings, drawing in cooler air from lower openings. Designing buildings with appropriate openings and layout to encourage cross-ventilation and stack effect utilization enhances natural ventilation.
D. Use of Awnings, Louvers, and Ventilation Openings
Architectural features such as awnings, louvers, and ventilation openings can aid in controlling the amount and direction of airflow. These features can be designed to allow for adjustable airflow, shading from direct sunlight, and protection from rain, while still promoting natural ventilation.
E. Balancing Natural Ventilation with Energy Efficiency
While natural ventilation offers benefits, it is essential to balance it with energy efficiency goals. Considerations include:
- Seasonal Variations: Designing for natural ventilation should account for different weather conditions, balancing the desire for fresh air with the need for thermal comfort during colder or hotter seasons.
- Control Mechanisms: Incorporating operable windows, vents, or automated systems allows for control over the amount and timing of natural ventilation, ensuring efficient use of energy.
- Integration with Mechanical Systems: Natural ventilation can work in conjunction with mechanical systems, such as HVAC systems, by utilizing mixed-mode ventilation strategies. This approach optimizes energy efficiency by combining natural and mechanical ventilation based on specific conditions and occupant needs.
By understanding the benefits and principles of natural ventilation, considering building orientation and window placement, utilizing cross-ventilation and stack effect, incorporating features like awnings and louvers, and balancing natural ventilation with energy efficiency goals, architects can create buildings that offer a healthy, comfortable, and sustainable indoor environment for occupants. Natural ventilation strategies contribute to improved IAQ, energy efficiency, thermal comfort, and a stronger connection between occupants and the natural elements.
V. Computational Fluid Dynamics (CFD) Analysis for Optimal Design
A. Introduction to CFD Analysis in Building Design
Computational Fluid Dynamics (CFD) analysis is a powerful tool used in building design to simulate and analyze airflow patterns, temperature distribution, and other fluid flow characteristics. CFD analysis provides insights into how air moves and interacts within a building, helping architects and engineers optimize ventilation and thermal comfort.
B. Simulating Airflow Patterns and Temperature Distribution
CFD analysis allows for the simulation of airflow patterns and temperature distribution within a building. By creating a virtual model of the building and defining boundary conditions, such as inlet and outlet openings, CFD software can predict the airflow paths, velocity, and temperature distribution. This information helps identify potential areas of stagnant air, heat accumulation, or thermal gradients.
C. Assessing Ventilation Effectiveness and Airflow Optimization
Through CFD analysis, architects can assess the effectiveness of ventilation strategies and optimize airflow within a building. By analyzing factors such as air velocities, flow rates, and ventilation efficiency, designers can identify areas where ventilation is inadequate or excessive. This information enables them to make informed decisions on modifying the building layout, adjusting opening sizes or positions, or incorporating additional ventilation mechanisms to improve airflow distribution.
D. Identifying Areas of Poor Air Circulation and Thermal Comfort Issues
CFD analysis enables the identification of areas with poor air circulation and potential thermal comfort issues. By visualizing airflow patterns and temperature distribution, designers can pinpoint areas where air stagnation, temperature stratification, or discomfort may occur. This information guides the optimization of HVAC system placement, adjustment of air outlet positions, or the incorporation of air deflectors to ensure better air circulation and thermal comfort throughout the building.
CFD analysis empowers architects and engineers to make data-driven design decisions, optimizing ventilation and thermal comfort while reducing the need for costly and time-consuming physical prototypes. By simulating airflow patterns, assessing ventilation effectiveness, and identifying areas of poor air circulation and thermal discomfort, CFD analysis helps create buildings that provide optimal indoor environments for occupants.
VI. Energy-Efficient Ventilation Solutions
A. Demand-Controlled Ventilation (DCV) Systems
Demand-Controlled Ventilation (DCV) systems optimize energy efficiency by adjusting ventilation rates based on actual occupancy levels and indoor air quality (IAQ) requirements. These systems use sensors, such as occupancy sensors or CO2 sensors, to monitor occupancy and IAQ indicators. When occupancy is low or IAQ is within acceptable limits, ventilation rates are reduced, resulting in energy savings. DCV systems ensure that ventilation is provided only when needed, preventing excessive energy consumption associated with constant ventilation rates.
B. Heat Recovery Ventilation (HRV) and Energy Recovery Ventilation (ERV)
Heat Recovery Ventilation (HRV) and Energy Recovery Ventilation (ERV) systems recover and reuse energy from exhaust air to pre-condition the incoming fresh air. HRV systems transfer heat from warm exhaust air to cool fresh air, while ERV systems also transfer moisture, helping maintain proper humidity levels. By recovering and utilizing energy that would otherwise be wasted, HRV and ERV systems reduce the load on heating and cooling systems, resulting in significant energy savings.
C. Efficient Fan and Motor Selections
The selection of efficient fans and motors is crucial for energy-efficient ventilation systems. High-efficiency fan designs and motors with low power consumption can significantly reduce energy usage. Variable speed drives (VSDs) can be integrated to modulate fan speed based on demand, further enhancing energy efficiency. Choosing fans and motors that are specifically designed for energy efficiency and matching them with the required airflow and pressure conditions ensures optimal performance and energy savings.
D. Integration of Ventilation with Building Automation Systems
Integrating ventilation systems with Building Automation Systems (BAS) allows for centralized control and coordination of various building systems, including HVAC and ventilation. BAS can optimize ventilation schedules, monitor indoor air quality, and adjust ventilation rates based on occupancy and environmental conditions. By integrating ventilation with BAS, energy efficiency is maximized, and ventilation operations are synchronized with other building systems for optimal performance.
Implementing energy-efficient ventilation solutions not only reduces energy consumption but also contributes to sustainable building practices and cost savings over the long term. Demand-Controlled Ventilation (DCV) systems, Heat Recovery Ventilation (HRV) and Energy Recovery Ventilation (ERV) systems, efficient fan and motor selections, and integration with Building Automation Systems (BAS) are key strategies in achieving energy-efficient ventilation. By adopting these solutions, architects can design buildings that prioritize energy conservation and provide a healthy and comfortable indoor environment.
Read also: Choosing Best Cement for Paver Block Manufacturing: A Comprehensive Guide
Conclusion: Optimizing ventilation and air circulation is a critical aspect of architectural building design, directly impacting indoor comfort and occupant health. By carefully considering the design of HVAC systems, ensuring good indoor air quality, harnessing natural ventilation strategies, utilizing CFD analysis, and promoting energy-efficient solutions, architects can create spaces that are comfortable, healthy, and sustainable.
-
Tech2 years ago
Best AC brands in India 2023
-
Uncategorized2 years ago
Optimizing Ventilation and Air Circulation in Architectural Building Design: Enhancing Indoor Comfort and Health
-
Uncategorized2 years ago
Choosing Best Cement for Paver Block Manufacturing: A Comprehensive Guide
-
Business3 years ago
Bhiwadi: An industrial city You Should Know About
-
Uncategorized2 years ago
Concrete blocks: Types, Tests Pros & manufacturing process
-
Tech3 years ago
E-waste Management Project: Effects, Challenges, and Solution
-
Business2 years ago
Solar Panels: 3 Types, Working & Manufacturing Process
-
Uncategorized1 year ago
11 – Aggregate Test -All Type & Importance